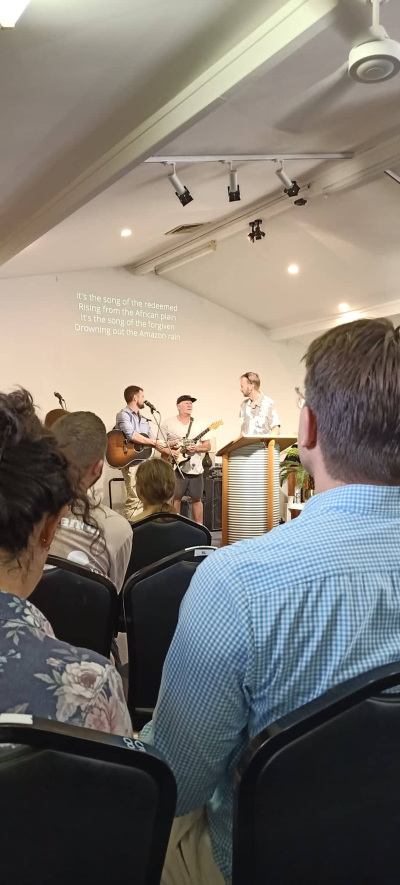
At the beginning of this year; at church, we started to have issues where our lighting washing out the projector and being too bight for those standing on stage (that's somewhat normal but it was too bright in this case).
In a proper theatre I'd just swap over to using par cans with barn doors however the stage lights we have are of more consumer/housing style and don't have any options for barn doors.
Without any commercial options for bar doors for our current lighting insulation I decided to design and 3D print a set of barn doors.
Design
I measured the light fixtures outer most diameter to get the size of the light. Using this measurement, I went with a simple design of a circular ring cut out of a square that can slip over the existing lighting fixture. To secure the ring to the lighting fixture I added two holes for a set of clapping bolts. The holes for the bolts were made to be tapping size for M4 bolts. I decided to print the barn doors as well. The barn doors would then held in place with a metal wire that was bent at both ends. The angle of the barn doors was a result of a educated guess based on a few photos of commercial fixtures (5.819 and 11.52 degrees for those playing along at home).
Materials & Printer
The lighting fixtures we are using get hot. Not hot enough to burn but probably hot enough to deform the PLA plastic that I was typically using with my 3D printer. So, for this task I decided to learn how to print with PETG. I chose PETG as it had the heat resistance along with the strength I needed for this project. I could have used ABS but my printer can't get safely hot enough and I don't have the correct ventilation to handle its fumes.
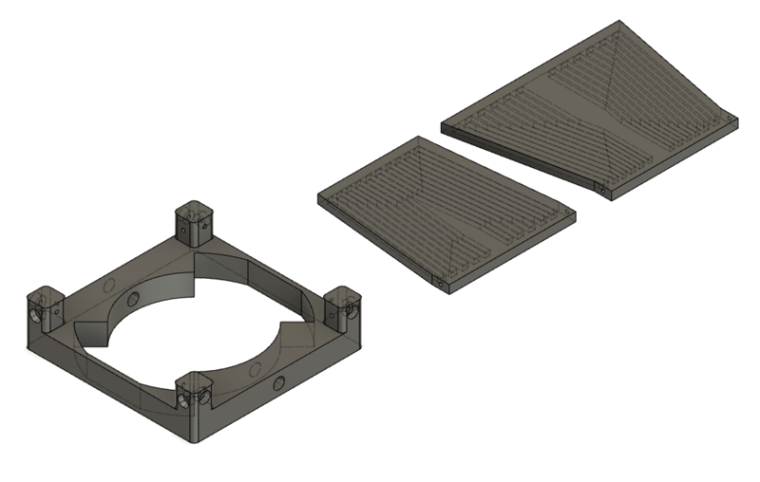
The printer I was running for this project was a modified Ender 3X. It was running a Micro Swiss all metal hot end and the glass bed. Halfway through the project I swapped back to the flex sheet bed because I was having issues with the PETG sticking to the glass print surface.
Printing and assembly
The first thing I did was print a test circular ring out of PLA so I could make sure that it fit correctly and the clamping bolts would work. When I got to church the ring was way too big. Looking at the measurements I had mixed up the measurements with a different lighting fixture. I went back to the drawing board and I used the correct diameter measurement and returned the following Sunday with a correctly sized part.
After that test, I the printed a single set of barn doors in PLA to make sure the light wasn't going to be too heavy for the mounting system. Once I was happy with all the parts in PLA I started the production print of six rings and barn door sets with PETG.
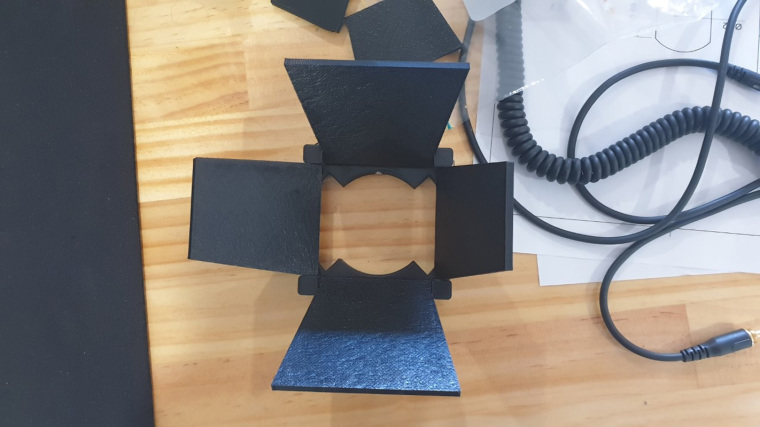
The PETG was giving me a lot of adhesion issues which left me with a number of warped parts that I couldn’t use. With the glass bed I tried adding some Glue stick but that only worked for one or two prints before the glass need cleaning, recoating and releveling. I decided to try the standard build surface that comes with the ender 3 and that resolved all my adhesion issues.
The printing was still slow. Each set of rings and barn doors took about 12 hours to print. That’s a total of 72 hours if done straight but in reality, it took a few weeks to fit all the printing around the other things in my life.
After the last part finished, I put the first one together and to my horror the barn doors just flopped about. This is when I realized the friction fit between PETG parts is a lot less than that of PLA parts. So, off to the hardware store I went to find a set of "external lock washers" to provided some friction so that the barn doors would stay in place; instead of flopping around. A after this little side trip I put the rest of the fixtures together.
A few Sundays later I installed the six set of barn doors and readjusted the lights so they evenly covered the stage. The end result was that our projector wasn't as washed out and it wasn't so blindingly bright for our musicians on stage.
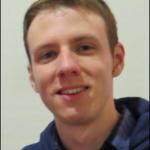
Zach Radloff is the Press Service International long serving IT young writer from the Gold Coast